AN AMAZING LITTLE POD!
An Amazing Little Pod!
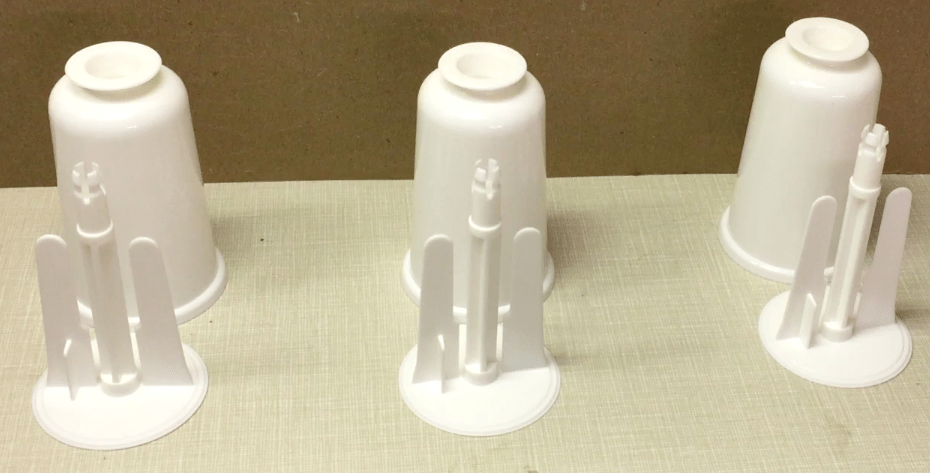
A growing challenge exists in the design & material selection of single-serve packaging. Primary design features of single-serve portion packs (SSPPs) emphasize the convenience and portability they provide as they are typically small in size and even in large quantity occupy minimal space. They easily store in cabinets or drawers. They travel well and are suitable for transport in a purse, briefcase, glove box etc. With minimal storage constraints, SSPPs provide fresh ingredients, accurately dosed at the place and time of use…what could be more convenient?
However, convenience gets negative press when viewed as having been prioritized over sustainability. Coffee pods in particular have received such reviews. Concerns of material usage and sustainability have routinely drawn SSPPs into their crosshairs. We’ve all seen pictures of plastic waste (some attributable to SSPPs) in landfills and oceans. Such waste is a horrible byproduct of our modern world. It needs to be and can be addressed.
Magnifying the challenge of environmental concerns, China, the world’s largest buyer of scrap plastic since 2011, just recently instituted its Green Fence policy, closing its doors to receipt of further scrap plastic. Though other developing nations have stepped up to fill the void created by China’s decision, none can handle the scale of material involved. Environmental management of many resins has been set back substantially as a result and forced Western nations to turn inward for solutions.
In addition, recycling in the United States has to own up to the fact that there are unacceptably low recycle rates for most resins. In most communities, less than 15% of the scrap plastics collected for recycling actually undergo a true recycling process, which often surprises people who are committed to recycling. The majority of the plastics are either incinerated or buried in landfills. Those plastics that do actually get recycled are contaminated with pigments and additives, inks, and adhesives. For injection molding, the resultant plastic granules are compromised with odors, colors, and substandard mechanical and physical properties. They are suitable for a very limited number of applications.
A handful of materials are used in the manufacture of SSPPs. Plastics are frequently chosen for their durability, moisture resistance, low cost, strength to weight ratio, recyclability, design flexibility and variety of usable formats. SSPPs employ plastics as single material films, films laminated to other substrate materials, sheets for vacuum forming and thermoforming, pellets or granules for injection molding and blow molding and possibly others of the myriad formats in which plastics are available.
Gudpod was faced with many of these considerations when evaluating materials for its Blender Pod. While committed to designs and materials that would minimally impact the environment, we concurrently strove to optimize the function of our Blender Pods for an unsurpassed user experience.
Highest among Gudpod’s performance requirements were that the material be low cost, light weight and exhibit strong barrier protection to light, moisture and oxygen while providing mechanical properties needed to enable required sealing, unsealing and re-closing forces and mixing dynamics. Whatever material was chosen had to be 100% recyclable and as environmentally friendly as possible. Gudpod ultimately selected a food grade polypropylene (PP) homopolymer. Lightweight, durable, flexible and with good barrier properties, PP is among the most widely used engineering resins available.
Owing to the benefits listed above, demand for recycled PP has never been higher, making it a leading candidate for investigation into alternate recycling technologies to increase recycling rates. As with the recycling of all resins, recycling of PP is hampered by the amount of pigments, inks, additives, adhesives and other contaminants that taint the granulated plastic particles prior to re-melting. Through a patented technology developed by Proctor & Gamble and its first licensee PureCycle Technologies, used PP resin will soon be reprocessed to near-virgin quality, eliminating all pigments, odors and contaminants. PureCycle claims they can recycle PP to nearly new condition, to be sold at market prices on a par with new material. It is estimated that present US annual demand for recycled PP exceeds 1 billion pounds and growing. So it’s understandable that PureCycle has undertaken to prototype the process in a facility about to go on-line in Lawrence, Ohio and plans to open a complete production facility in 2020.
Gudpod is very encouraged by its cutting-edge material selection of food grade, homopolymer PP. Not only have we chosen a material that meets our customers’ needs and delivers quality and performance, we have aligned ourselves with the first resin that will be reprocessed in a verifiable, legitimate recycling effort. Particles that were once part of our injection molded Blender Pods will be able to be reborn in near virgin condition as a fresh clean batch of molding resin, ready to be pigmented and blended with additives as the resin undergoes a true reprocessing cycle.
Metals are routinely sold as scrap and reprocessed for re-use. Scrap metal is seen as a source of revenue by the seller and reprocessor, not as a source of waste. As more advanced and comprehensive plastics recycling programs get underway, fewer plastics will find their way into our waterways and landfills. These materials will be viewed like scrap metals as sources of revenue, valuable to recyclers and practical for re-use.
Gudpod is dedicated to its policy of balancing exceptional product performance with prudent stewardship of planet Earth and her limited resources. We will continue our investigation of materials and design in pursuit of a truly compostable pod. We’ll experiment with many different resin types including bioplastics whose carbon is derived from renewable sources such as corn, sugar and starch. (Such materials introduce minimal supplemental carbon into the atmosphere as compared to those whose carbon derives from fossil fuel sources which contain carbon that has been inert for geologic time frames.) Our R&D brainstorming sessions entertain all manner of areas for further development…even edible packaging which is truly food for thought!
It’s like we’ve been saying for a while… Güd things are happening… stay tuned! #gudthingsrhappening #gudpod #personalizednutrition #innovation #precisiondosing
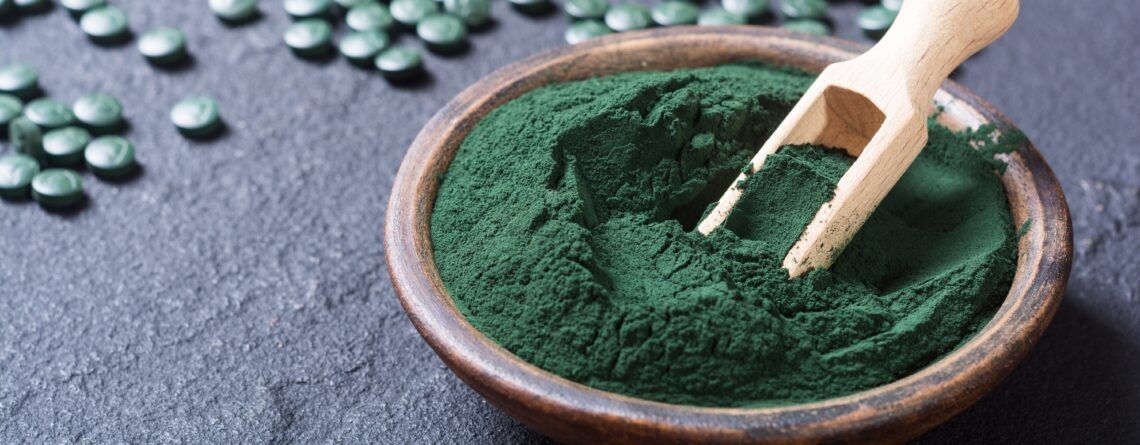